Where Theory Meets Practice
A look inside ENG’s new design and manufacturing facility
The Engineering Product Innovation Center (EPIC) has been open for less than a year, and it’s already become the tinkerer’s paradise. On any given day, the machine shop hums and clinks with life as students, faculty, and staff from across campus transform ideas into actual things. Engineers rub shoulders with sculptors, sculptors with biologists, and biologists with rocket scientists as they share the shop’s machines with the help of experienced EPIC staff members and student workers.
“We believe that engineering education in this country is in need of an upgrade, and we want to be leaders of it,” says EPIC director Gerry Fine, a College of Engineering professor of the practice.

Matt Ramirez (ENG’17) aligns material within one of EPIC’s three computer numerical control (CNC) machines.
The 15,000-square-foot facility at 750 Commonwealth Ave. houses computer-aided design (CAD) software and computer-aided manufacturing (CAM) technology, 3-D printers, laser processers, a robotic assembly line, and a variety of machining tools—including lathes, millers, and good old-fashioned drills and saws. John Tegan (ENG’88) recently donated funds to name the large design room the Lorraine A. Tegan Design Studio. A separate materials characterization lab, metals foundry, circuitry studio, and carpentry shop complete the first floor space. General classrooms fill the second floor.
EPIC was made possible through a partnership with principle industry sponsors GE Aviation, Procter & Gamble, PTC, Rolls Royce, and Schlumberger. Laboratory Supervisor Joseph Estano keeps the facility open seven days a week and has a staff of four full-time employees and 16 student workers scheduled throughout the day to help visitors.
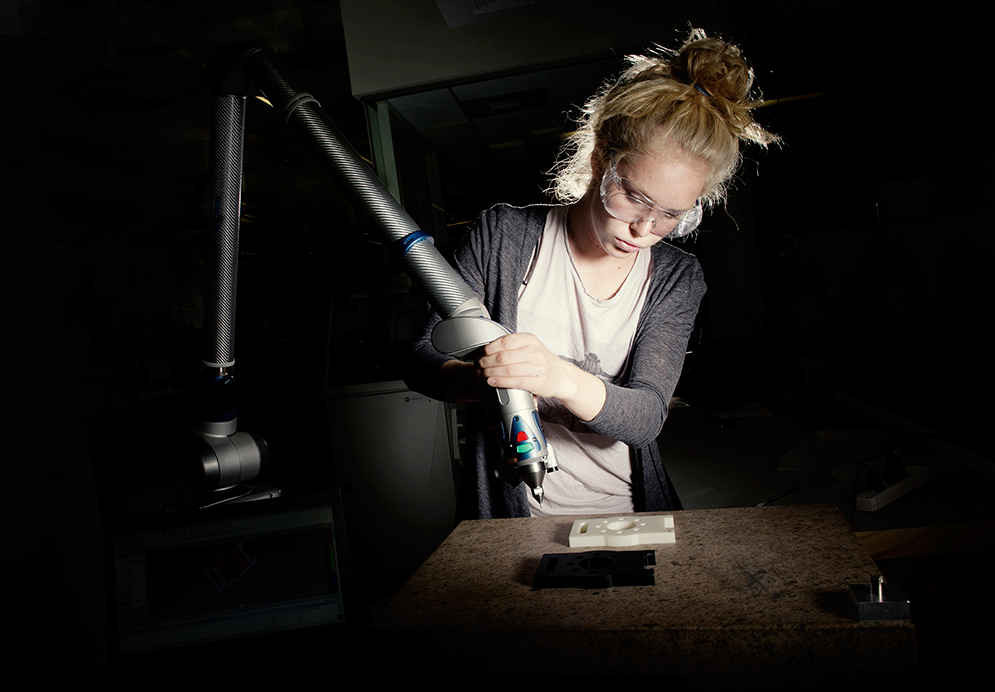
Hester Van Der Laan (ENG’17) passes a Faro Edge ScanArm over a milled project to produce a 3-D image for quality control purposes.
On a recent afternoon in the glass-walled space, EPIC student worker Vincent Celeste (ENG’16) huddled with Scott Nickelsberg (ENG’17) and Walid El Kara (ENG’17) at a bank of computers as he helped them convert their 3-D model of a gyroscope to GibbsCAM CAD/CAM software. The project was an assignment for their manufacturing design class (EK 156) with Theo de Winter, an ENG associate professor of mechanical engineering.
“The only requirements were build something,” Nickelsberg said.
“And do it in EPIC,” Elkara added.
The two had considered building a gumball machine or a guitar stand, but after consulting EPIC Senior CIMLAB Specialist Bob Sjostrom, they decided the simpler route would be a gyroscope. On the computer screen before them, Celeste had mapped out each piece of their project so that it fit on a single square of their raw material, low-carbon steel.
This Is EPIC! By Caleb Daniloff. Video by Casey Atkins and Devin Hahn.
Doctoral candidate Tim Jackman (ENG’15) believes that the answer to preventing a common back injury—wedge fractures that typically result from heavy lifting—lies in calculating the amount of stress that human vertebrae can withstand. So from his workstation at BU’s Orthopaedic and Developmental Biomechanics Laboratory, he has reached out to the folks at BU’s Engineering Product Innovation Center (EPIC).
Starting with sketches on paper, Jackman and a staffer at the new design and manufacturing studio created a tube with a screw top that could exert pressure until the vertebrae crushed. After compiling the data from his experiments, he hopes to create computer models to identify people who would be at immediate risk for fractures.
Doctoral candidate Tim Jackman (ENG’15) believes that the answer to preventing a common back injury—wedge fractures that typically result from heavy lifting—lies in calculating the amount of stress that human vertebrae can withstand. So from his workstation at BU’s Orthopaedic and Developmental Biomechanics Laboratory, he has reached out to the folks at BU’s Engineering Product Innovation Center (EPIC).
Starting with sketches on paper, Jackman and a staffer at the new design and manufacturing studio created a tube with a screw top that could exert pressure until the vertebrae crushed. After compiling the data from his experiments, he hopes to create computer models to identify people who would be at immediate risk for fractures.
After adjusting a few measurements, Celeste asked his coworker Solange Coughlin (ENG’15) to review his work before sending it to an automated mill. “I don’t know if it’s going to fly around, but it would probably knock someone out,” Coughlin said, pointing to the pieces she felt needed adjustment. She advised tweaking the dimensions even more; Sjostrom looked over their shoulders and nodded his approval.
Another pair of de Winter’s students, Regina Czech (ENG’17) and Mariam Omar (ENG’17), stood at a workbench alongside a box-like computer numeric controls (CNC) milling machine, nicknamed “Porthos.” (EPIC staff named each CNC milling machine after characters in Alexandre Dumas’ The Three Musketeers.) The two students were building a palm-sized sliding puzzle from high-density polyethylene and were inspecting milled pieces for flaws.
“This is the first time they’ve left us alone with the machine,” Omar said. “We haven’t broken anything yet. They told us where the big emergency button is.” Smiling widely, she pointed to a large red knob on the front of the machine.
Czech and Omar had run into a temporary roadblock when they weren’t able to mill perfectly square-edged, interlocking pieces. Coughlin showed them how to change the orientation of their raw material within the machine to achieve their desired cut.
“They’re making a really big effort to make us feel we can do it ourselves,” said Czech, who hopes to become an EPIC student worker someday.
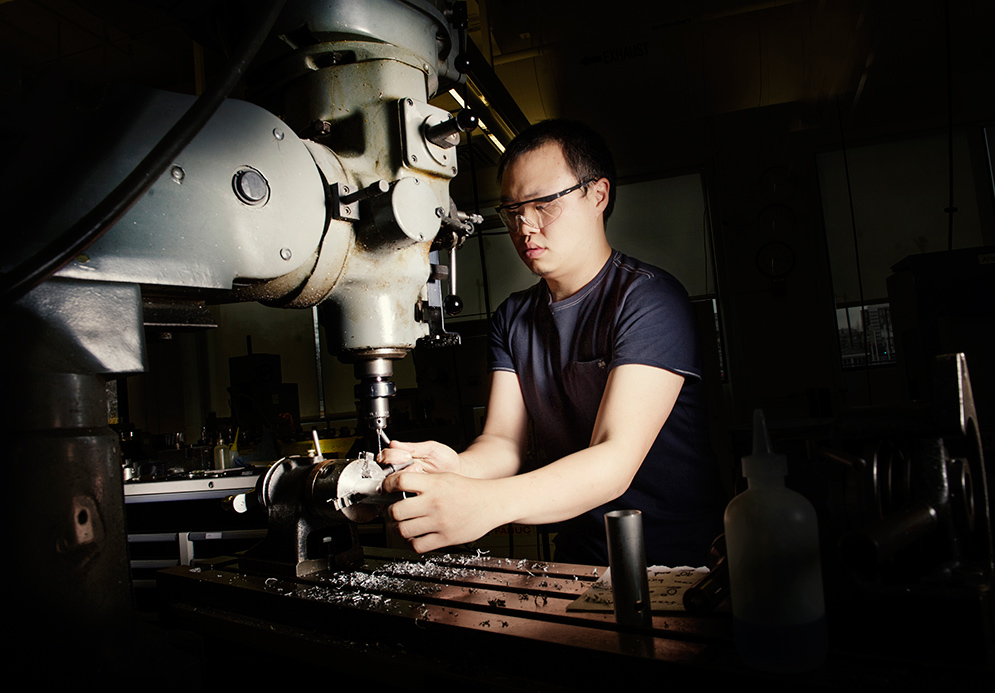
Brandon Wong (ENG’17) guides a manual milling machine to make a housing block.
Across the room, David Sindel (ENG’15) guided a long steel rail onto the platform of a manual mill and methodically drilled four pairs of half-inch diameter holes down its spine. The piece would be bolted to an old trailer that he and other members of the Boston University Rocket Propulsion Group were converting into a main test stand for their 32-foot-long rocket. They plan to begin an extensive test campaign for the rocket in January, make a few more tweaks to the design, and aim for a July launch. If successful, their club will have produced the first amateur-built rocket to shoot 140 kilometers into space, and the first built by a university group.
A stone’s throw away, Josh Zins (ENG’17) used a lathe to shave a quarter-inch from the diameter of six steel shafts for a project in Fine’s introduction to engineering design class (EK 210). Their client, Schlumberger, was having problems with vibration in a horizontal well drill and the company suggested students brainstorm solutions using EPIC software and machines.
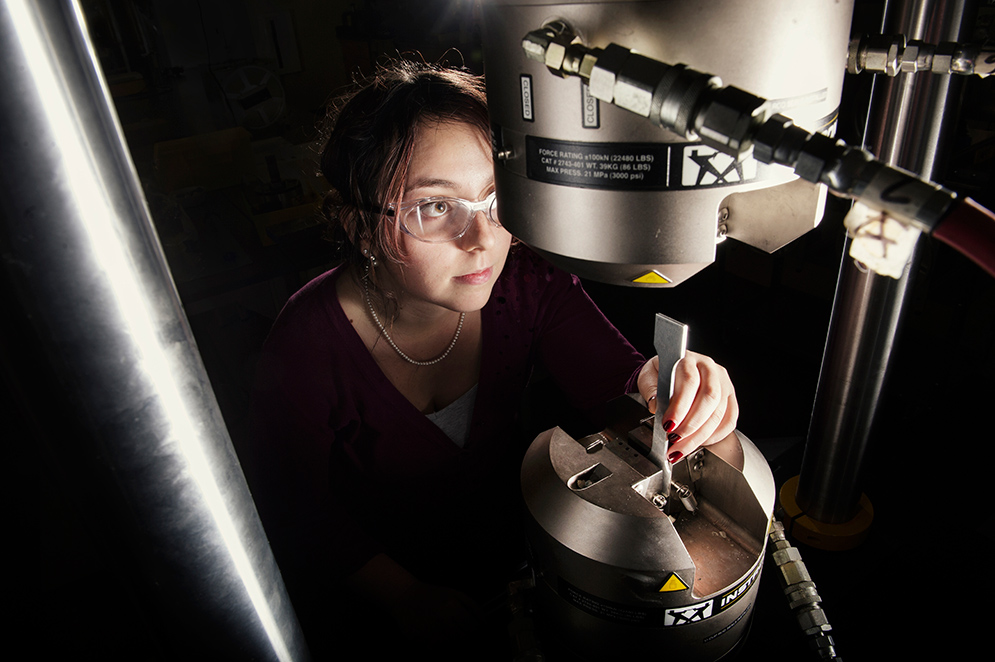
Anna Burkatovsky (ENG’16) demonstrates the Instron tensile and compression test apparatus within EPIC’s materials characterization lab.
Zins’ group had come up with a potential design solution, so he spent a good portion of the afternoon preparing steel shafts that would become part of a clamp in the drill casing. He carefully fastened each shaft into the lathe, checked its settings, and set the machine in motion. Curlicues of steel peeled off each shaft and fell like silver confetti into a catch basin below.
Yingxian “Estella” Yu (ENG’15) and Jon Hoxha (ENG’15) hunched over a miniature lathe that served as one of several stops along the robotic assembly line. They had been given a remote control car and told to keep the motor and electronics, but redesign the chassis and body as part of their automation and manufacturing methods class (ME 345) with Peter Zink, an ENG research assistant professor in mechanical engineering.
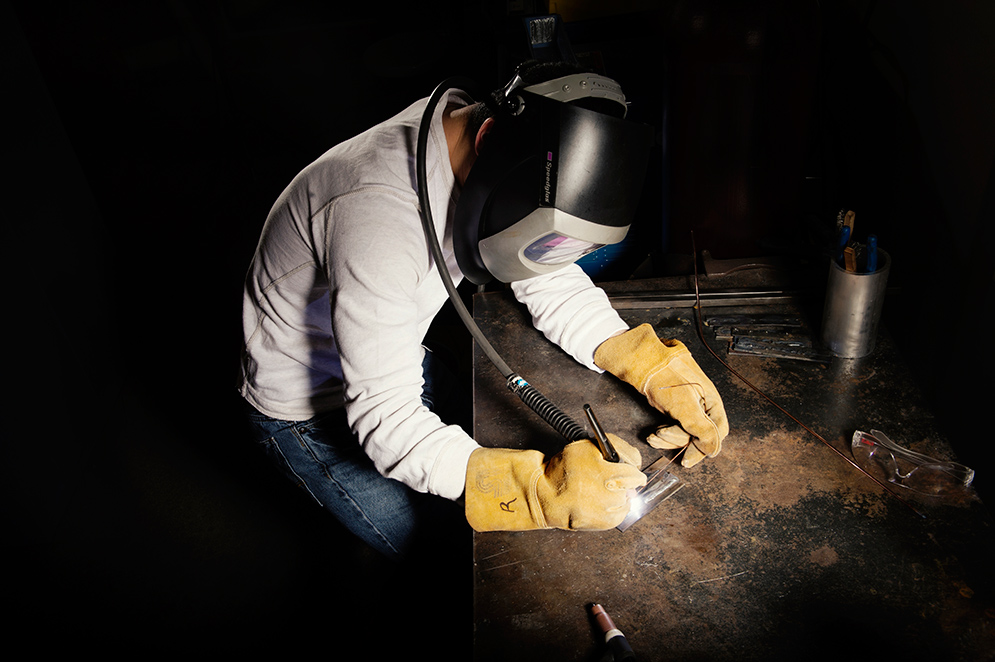
Vincent Celeste (ENG’16) expertly welds metal within one of EPIC’s first floor studios.
Yu and Hoxha had been polishing up their design and converting it with GibbsCAM CAD/CAM software, when they took a break to figure out how to attach their raw material onto the small lathe. At the end of the semester, when their chassis and body are complete, they’ll assemble the car and race it against their classmates’ models.
Lab supervisor and machinist Ryan Lacy (ENG’12,’14) chatted with Zink alongside the robotic arm assembly, which has a prominent spot facing EPIC’s glass-paned façade. Asked if their work ever generated a crowd on the sidewalk outside, Lacy nodded with an impish grin. He’s often thought of asking his audience: “Are you guys going to get to class on time?”
EPIC is open Mondays through Thursdays from 8 a.m. to 10 p.m.; Fridays from 8 a.m. to 6 p.m.; and Saturdays and Sundays from 10 a.m. to 6 p.m.
Comments & Discussion
Boston University moderates comments to facilitate an informed, substantive, civil conversation. Abusive, profane, self-promotional, misleading, incoherent or off-topic comments will be rejected. Moderators are staffed during regular business hours (EST) and can only accept comments written in English. Statistics or facts must include a citation or a link to the citation.